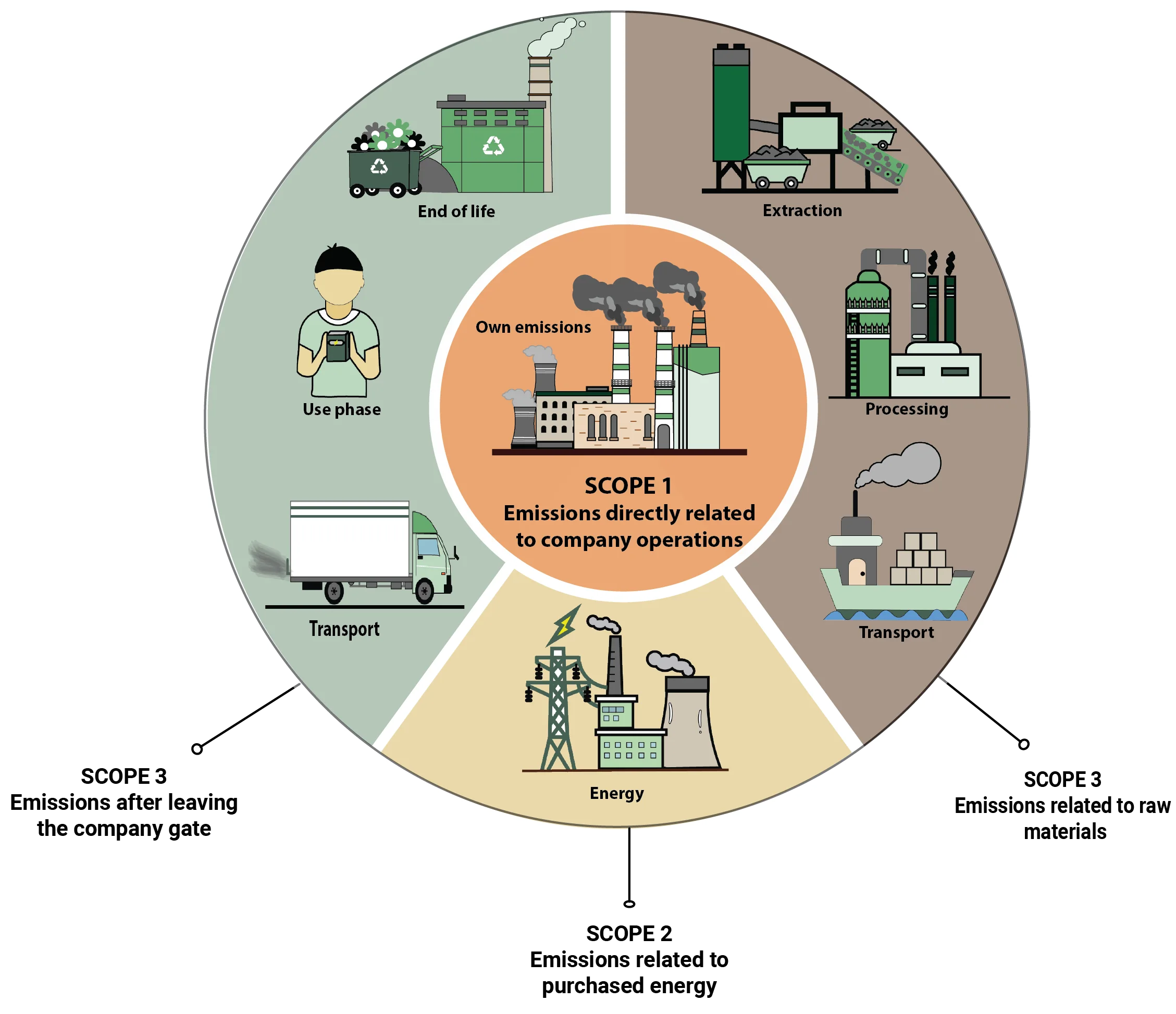
Product Carbon Footprint (PCF) Reporting Software
How to meet your reporting obligations and decarbonise with company-specific data at a product level.
What is a Product Carbon Footprint (PCF)? Definition and Explanation
In short: A PCF measures the total greenhouse gas emissions (CO2e) associated with a product’s entire lifecycle, from raw material extraction to end-of-life disposal.
Product Carbon Footprint (PCF) Definition:
A PCF is a quantitative measure of the total greenhouse gas (GHG) emissions, expressed in carbon dioxide equivalent (CO2e), associated with a product’s entire lifecycle, from raw material extraction to end-of-life disposal or recycling. PCF encompasses the assessment of GHG emissions across various stages, including:
- Raw material extraction and processing
- Manufacturing and production
- Transportation and distribution
- Use and consumption
- End-of-life management (disposal, recycling or reuse)
PCF calculations can be applied using different system boundaries, including:
- Cradle-to-Gate: Emissions generated from raw material extraction to the point of product manufacture, including precursor production, up to the point where the product leaves the company gate.
- Cradle-to-Grave: Emissions generated across the entire product lifecycle, including use and end-of-life phases.
Note: Accurate PCF calculations rely on selecting the appropriate system boundary, which depends on the organisation’s goals, product complexity and supply chain characteristics.
PCF key characteristics:
- PCF differs from corporate-level carbon footprints by focusing on product-level emissions rather than aggregating emissions across an entire organisation.
- PCF employs the Life Cycle Assessment (LCA) methodology, which evaluates a product’s environmental impacts across its entire lifecycle. PCF specifically focuses on greenhouse gas emissions and global warming potential.
- Accounts for direct and indirect GHG emissions across the product’s entire lifecycle.
- Provides a comprehensive understanding of a product’s carbon impact.
- Enables informed decision-making for product design, supply chain optimisation and climate strategy.
Note: PCF typically encompasses Scope 3 emissions, categorised into upstream, downstream and other indirect emissions, as defined by the GHG Protocol.
Product Carbon Footprint Lifecycle Stages
Below is a visual representation of the greenhouse gas emissions generated across a product’s lifecycle, categorised by lifecycle stages and scope emissions as defined by the Greenhouse Gas Protocol.
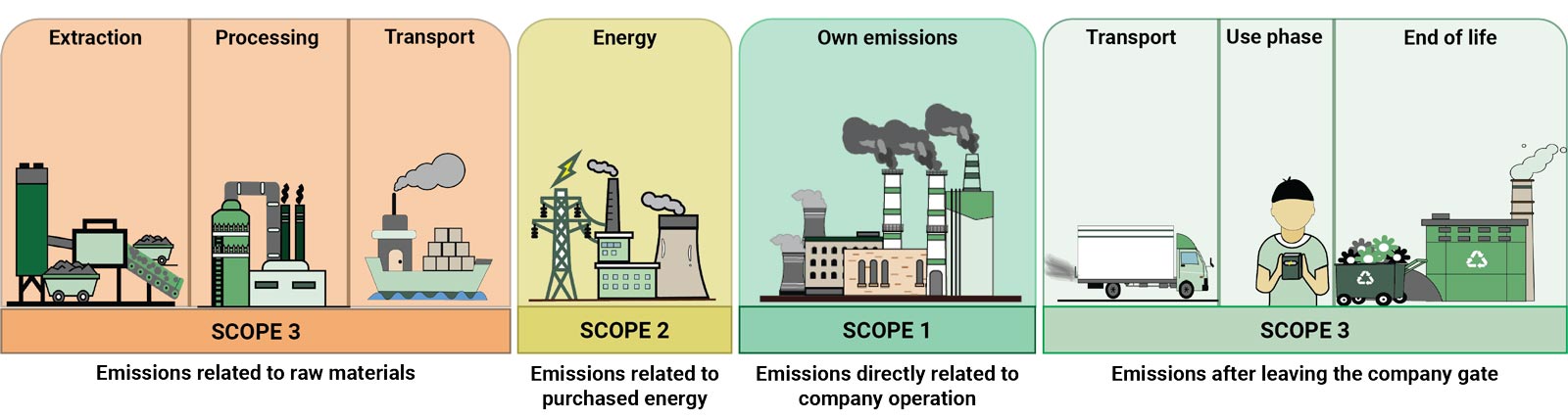
Why calculating a Product Carbon Footprint (PCF) matters
As customers, regulators and stakeholders increasingly demand transparency down to an individual product level, accurate Product Carbon Footprint (PCF) data is now essential for industrial operations to maintain competitiveness and compliance.
Key drivers include:
- Market demand and competitiveness: Consumers are prioritising lower-carbon products, driving demand for verifiable environmental credentials.
- Compliance: Emerging legislation, such as the EU Carbon Border Adjustment Mechanism (CBAM), EU Batteries Regulation and UK CBAM, requires PCF reporting.
- ECO-labelling and certification: PCF data supports the growing use of eco-labels, like EPEAT, enhancing market reputation and credibility.
- Stakeholder engagement: PCF calculation facilitates collaboration with suppliers, clients and stakeholders.
- Risk management and future proofing: Proactively addressing environmental impacts prepares businesses for upcoming regulatory obligations.
Increasing product carbon footprint (PCF) legislation
While most mandatory sustainability reporting is currently at a corporate level, legislation and taxes are increasingly requiring companies to report down to a product level.
Notable examples of this shift include the EU Batteries Regulation, the EU Carbon Border Adjustment Mechanism (CBAM) and the UK and AU CBAMs. This legislation and others share the goal of reducing environmental impact. However, their PCF calculation methods differ significantly regarding the boundaries of what is included, the lifecycle stages considered, and the impact categories assessed.
Understanding these emerging regulations is crucial for ensuring compliance and staying ahead.
Related: The rise of product carbon footprint (PCF) legislation
What methods are used to calculate a PCF?
Calculating a PCF involves various methodologies and scopes driven by evolving international legislation and carbon tax schemes.
PCF is a subset of Life Cycle Assessment (LCA), which focuses on climate impact, while other methods encompass broader environmental issues.
As energy-intensive industrial operations must comply with the regulations applicable to their industry, operation and region, understanding the relevant PCF calculation methods is crucial. Key methodologies include:
- ISO 14067: Provides an international reference standard for PCF calculation, focusing on greenhouse gas emissions.
- PAS 2050: Assesses life cycle greenhouse gas emissions, widely used internationally.
- GHG Protocol Product Standard: Offers a comprehensive framework for PCF calculation, including public reporting requirements.
- Product Environmental Footprint (PEF): EU-recommended method for LCA, covering 16 impact categories, aiming to standardise environmental performance assessment.
- National standards (e.g., BP X30-323-0, EN 15804): Provides industry and country-specific guidelines for PCF calculation.
Despite varying methods, compliance and reporting requirements, all PCF calculations rely on accurate, standardised and auditable data, making digital data-driven tools essential.
Your digital roadmap to PCF compliance
Whether you are just starting PCF calculations or already have PCF reporting and compliance processes and targets in place, digital PCF reporting software can help at every stage.
Starting by centralising your data, the right digital tools are the only way to address today’s mandatory requirements, adapt to evolving legislative frameworks and help set and achieve decarbonisation targets and lower carbon footprints.
For complex industrial organisations, ISS recommends a staged roadmap to PCF digital reporting that starts with meeting mandatory compliance rules and moves towards advanced ESG capabilities and emissions reduction strategies as your capabilities mature.
There are four critical steps in the recommended roadmap that align with our Sustainability Tracker (ST) packages:
Centralise data
Centralise data and use templates to meet today’s compliance regulations.
Set up the systems needed for centralised records that capture the in-depth PCF activity data needed to adjust to varying PCF reporting requirements.
Define the system boundary/boundaries according to the PCF/LCA/Environmental Footprints (EF) calculation methodologies you are required to report to. For example, cradle-to-grave or/and cradle-to-gate.
Automate data capture
On top of centralised data, the next step is to add automated data capture and data quality to your PCF/LCA reporting.
This includes data cleansing, organisation and validation tools (using machine learning), and advanced visualisation tools to deliver dynamic, accurate and auditable near real-time PCF/ LCA reporting.
Finance-grade reporting
Beyond automation, the next step is enabling finance-grade PCF/LCA reporting and automated validation of PCF/ LCA data against industrial operations data using a mass and energy balance configured to your site/s.
You can report various PCF calculation methodologies required by legislation such as the EU Batteries regulation carbon footprint declaration. Adjust calculations for CBAM to include in-scope indirect, direct and precursors emissions.
Adjust calculations according to various standards such as the GHG Protocol Product Standard and the EU PEF.
Decarbonisation roadmap
The final step is adding the granular analysis needed to plan, execute and evaluate your decarbonisation roadmap at a product level.
Compare your PCF to others in the market and plan ways to lower your PCF to become a market leader.
Running a steady-state simulation of your asset, validated finance-grade industrial data is used to enable complex forecasting, transition planning, scenario analysis and climate resilience assessments.
You can then adjust inputs and compare final production, emissions and consumption using advanced visualisation tools.
Product Carbon Footprint (PCF) Reporting Standards
With differing PCF standards available, selecting the right one depends on the intended use, industry and regulations, including rules specific to region, sector and product.
Whether for public reporting, green claims, legislative compliance or carbon taxation, it is crucial to understand the applicable standards, their applications and characteristics.
PCF standards at a glance
Standard | Application |
ISO 14067 | The internationally recognised standard if no specific regulation is to be followed. |
PAS 2050, BP X30-323-0 | PAS 2050 focuses on providing a ‘consistent method for assessment’. PAS 2050 review has introduced ‘supplementary requirements’ (SRs) that include sector guidance/rules and product Category Rules. |
EN 15804, Product Category Rules | Defines how companies, especially in construction, should create Environmental Product Declarations (EPDs) |
GHG Protocol Product Standard | Product Standards ‘account for and publicly report GHG inventories of products’. The Product Standard refers to ‘product rules’ to enable comparisons. |
EU Product Environmental Footprint (PEF) | A method to measure the environmental impacts across the lifecycle of products in 16 impact categories with more to come. |
Why digital reporting is the only solution for PCF reporting
The need for product carbon footprint reporting across hundreds of specific data points and several calculation methodologies and standards means that data-driven technology is the only solution to meet evolving LCA, PCF and environmental footprint (EF) standards.
Manual spreadsheets cannot capture or process the volumes of data needed to deliver footprints at the product level.
The good news is that digital tools proven to solve these data challenges for complex industrial organisations are available.
Examples of using Sustainability Tracker (ST) PCF reporting software
These examples demonstrate how Sustainability Tracker (ST) PCF reporting software can satisfy PCF compliance and help achieve decarbonisation goals with granular reports calculated to meet various methods and legislation, such as the EU Batteries Regulation.
EU Batteries Regulation – Carbon Footprint Declaration
EU Batteries Regulation requires companies to measure and report a carbon footprint declaration for EV batteries, rechargeable industrial batteries and LMT batteries.
In this example we demonstrate how ST reports on the lifecycle carbon footprint stage ‘Raw material acquisition and pre-processing’ for a producer of lithium products used as a raw material by a battery manufacturer.
Lithium raw material carbon footprint declaration
Example data points to be reported as per Article 7(1) of Regulation (EU) 2023/1542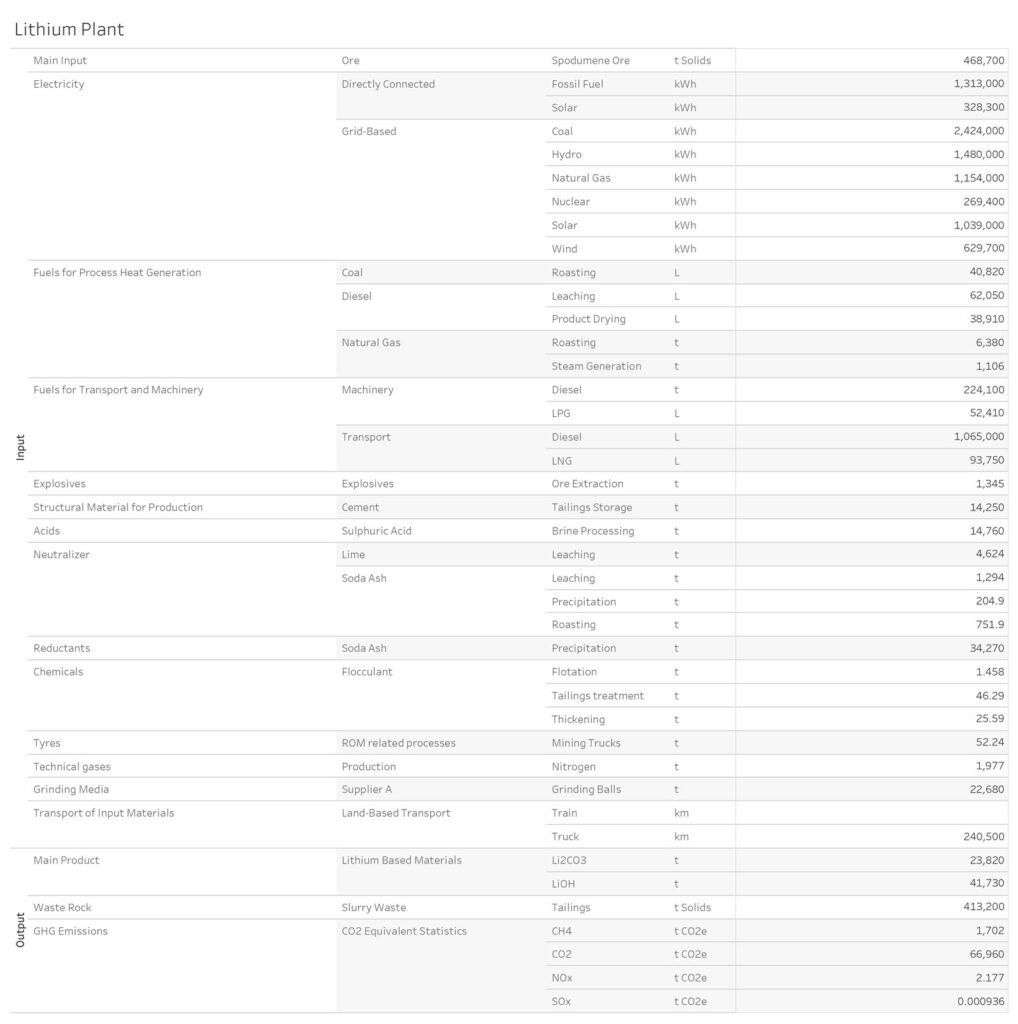
Deep dive into main input or output category of the EU Carbon Footprint Declaration
Electricity at a granular level
Behind the aggregated data as per the carbon footprint declaration are the consumption data for each category and fuel type by month.
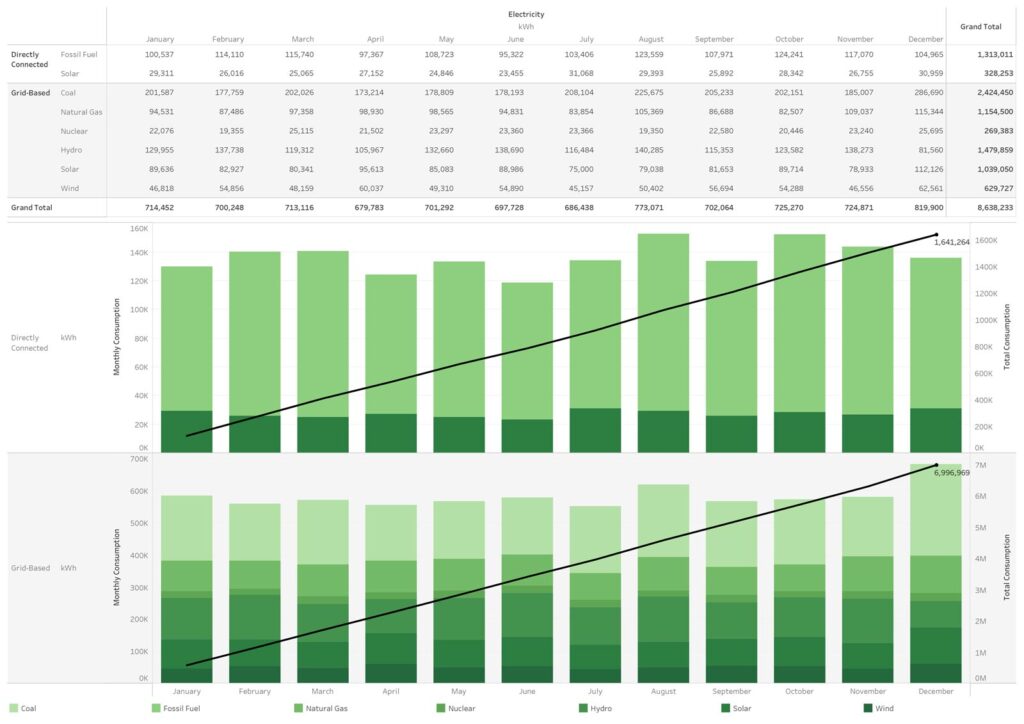
Fuels for process heat generation
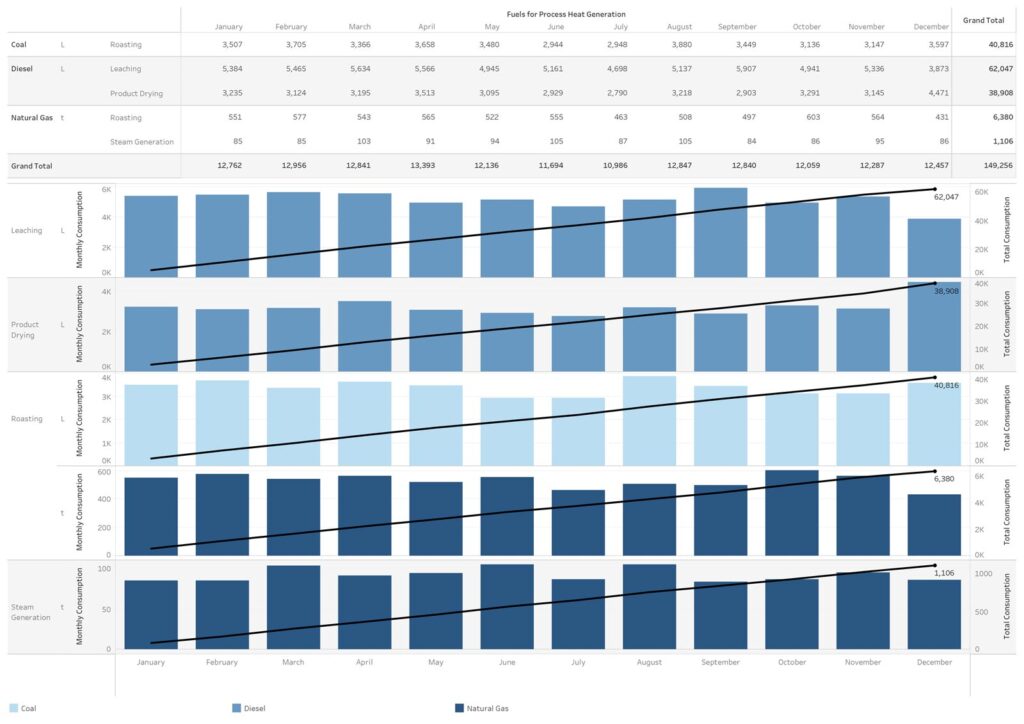
Fuels for transport and machinery
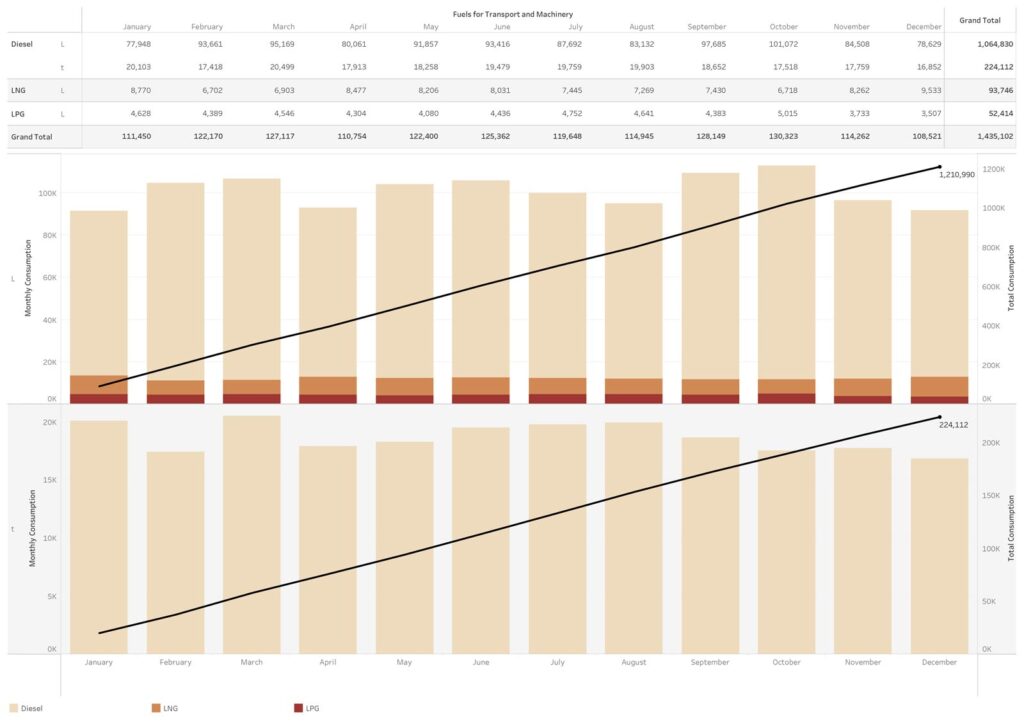
Greenhouse Gas Protocol: Product Life Cycle Accounting and Reporting Standard
Using ST, companies can measure the greenhouse gases associated with the full life cycle of products including raw materials, manufacturing, transportation, storage, use and disposal.
The data analysis can be used to create competitive advantage by enabling better product design, increasing efficiencies, reducing costs and removing risks.
Emissions by individual product
- Emissions reported at a product level by scope 1, 2 and 3
- Scope 1 is broken down into emissions sources and fuel type
- Scope 2 is broken down by energy type and location and market-based methods
- Scope 3 is reported by categories and by fuel and reagents
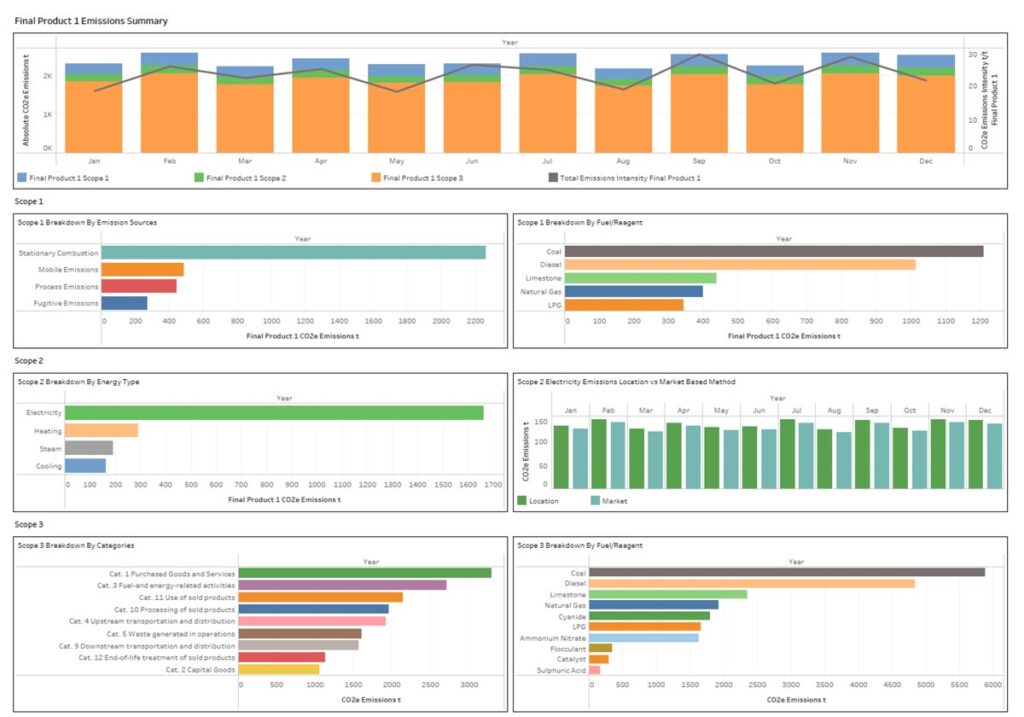
Assurance / Verification
Carbon footprint declarations need to be verified and validated. The data needs to be accurate, immutable, auditable and unalterable.
Assurance Report:
Traceability is crucial under the Regulation. This is an example of the audit trail in the activity feed of ST that details any changes or modifications to data.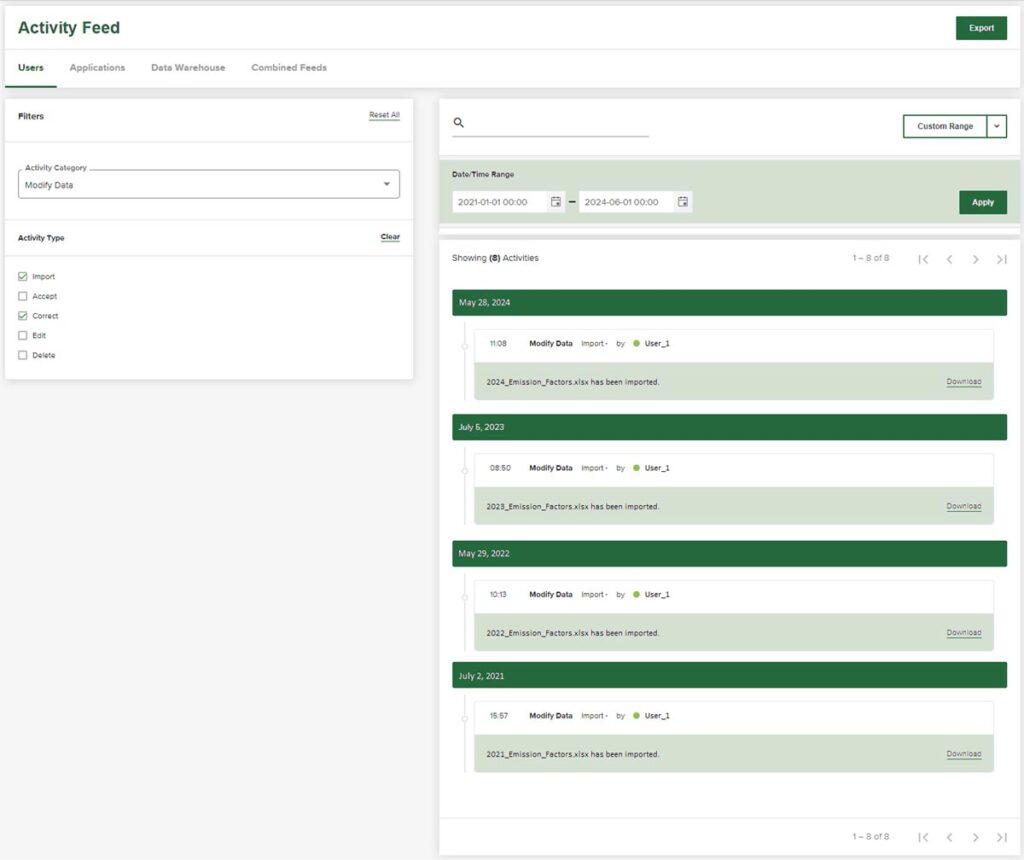
Digital Battery Passports
Starting 1 February 2027, the EU’s Battery Passport Regulation requires all electric vehicle and industrial batteries to carry a unique QR-coded passport.
Battery Passport Electronic Reporting format:
To comply, companies must track each battery throughout its lifecycle, aggregating data on production, usage, and end-of-life.
A digital battery passport is crucial for seamless compliance. It enables:
- Secure sharing of sensitive information across supply chains
- Verification of data reliability and validity
- Real-time tracking and reporting
The digital format ensures data integrity, confidentiality, and trust among stakeholders. The example below illustrates a digital battery passport.
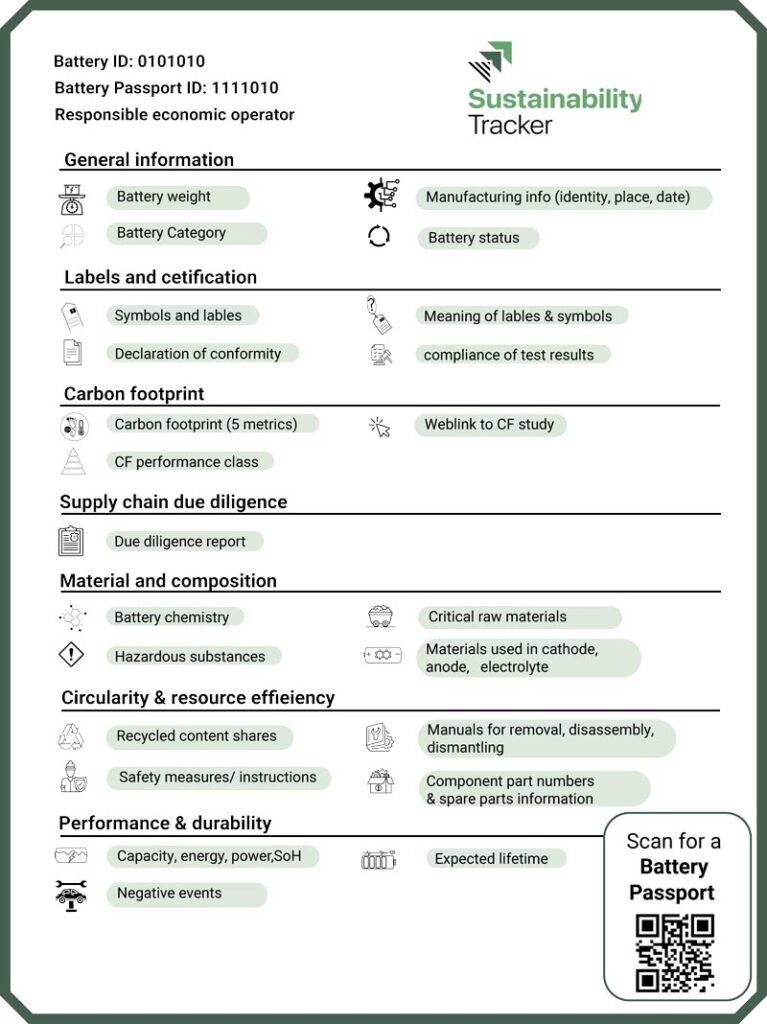
PCF Frequently Asked Questions
What is a Product Carbon Footprint (PCF)?
PCF is a quantitative measure of the total greenhouse gas emissions (expressed in carbon dioxide equivalent, CO2e) associated with a product’s entire lifecycle, from raw material extraction to end-of-life disposal or recycling.
What organisations need to calculate PCFs?
PCF calculations and reporting increasingly apply to businesses across various sectors, particularly carbon-intensive industries. Specific regulations like the EU Batteries Regulation apply to manufacturers of electric vehicle batteries, rechargeable industrial batteries, and light means of transport batteries. The EU and UK Carbon Border Adjustment Mechanisms (CBAM) apply to importers of certain carbon-intensive products.
What needs to be reported in PCFs?
PCF reporting typically includes emissions from all stages of a product’s lifecycle: raw material extraction and processing, manufacturing and production, transportation and distribution, use and consumption, and end-of-life management. The specific reporting requirements can vary based on the applicable regulations and chosen calculation methodology.
What are the benefits of PCF reporting?
PCF reporting benefits include meeting regulatory requirements, improving market competitiveness, supporting eco-labelling and certification, enhancing stakeholder engagement, managing risks, and preparing for future regulatory obligations. It also enables businesses to identify areas for emissions reduction and improve overall sustainability performance.
What are the risks of non-compliance with PCF requirements?
Not meeting PCF requirements can include regulatory penalties, loss of market access (particularly in regions with strict environmental regulations), reputational damage, reduced competitiveness, and missed opportunities for operational efficiency improvements and cost savings.
Why are spreadsheets not suitable for PCF reporting?
Many industrial plants continue to use spreadsheets to perform sustainability reporting. However, given the complexity of data, multiple data points and the requirement that reports need to be provided in an auditable electronic reporting format to be compliant, spreadsheets can no longer keep pace. Error-prone and time-consuming, using spreadsheets exposes risks. Without the right data-driven sustainability platform, it’s impossible to meet PCF reporting requirements, let alone implement effective decarbonisation strategies.
How does Sustainability Tracker (ST) help with PCF reporting?
Sustainability Tracker simplifies PCF reporting with a user-friendly interface, providing a comprehensive framework that covers all necessary disclosures. It automates data collection and calculation to reduce manual effort in producing reports in the required PCF digital format. ST also enables companies to set targets, track progress and benchmark performance.
The Sustainability Tracker difference
Designed to navigate multiple global frameworks and many separate ESG performance indicators, Sustainability Tracker is a uniquely flexible and comprehensive sustainability reporting solution for today and the future.
Whether you are just starting your sustainability journey or already have sustainability reporting and compliance processes and targets in place, ST has a flexible package for every stage.
The below benefits span from ticking sustainability compliance boxes on our Standard Package right through to advanced environmental, social and governance (ESG) capabilities on our Expert and Enterprise Packages:
- Track end-to-end sustainability indicators spanning Scopes 1, 2 & 3, and Climate & Nature
- Single source of centralised, validated, organised and integrated sustainability data
- Accurate asset-wide mass and energy balance customised to your exact process as a digital replica of your operations
- Contextualise your measured activity data using source data as inputs
- Analyse, track and report activity data right down to a product level
- Track and consolidate on-site and off-site renewable energy sources
- Capture and report on data directly related to the industrial asset it has been implemented in, including integration with third-party data
- Track, simulate, test, analyse and forecast scenarios
- Future-proof technology delivered in a scalable cloud-based SaaS platform
Take control of your product carbon footprint (PCF) reporting
To learn how Sustainability Tracker (ST) can help you meet your PCF reporting obligations and minimise emissions, energy, water and waste across your supply chain, contact our expert team on +61 2 7229 5662 or info@industrialsustainabilitysolutions.com
More sustainability reporting resources
About the Authors
This article has been collaboratively authored by the Industrial Sustainability Solutions team and fact-checked and authorised by Managing Director and industry specialist John Vagenas.