With demand for critical minerals on the rise, our sustainability software helps a prestigious scientific organisation develop a carbon reduction strategy.
Across the globe, more consumers and businesses are transitioning to clean energy and switching to electric vehicles. This exponential electrification of everyday life is creating a surge in demand for batteries and battery storage, not to mention the critical minerals used to produce them.
For example, a recent McKinsey study projects that the entire lithium-ion (Li-ion) battery chain, from mining through recycling, could grow by over 30 percent annually from 2022 to 2030. An International Energy Agency study predicts demand for critical minerals involved in battery production — like cobalt and nickel — to grow by up to 25 times by 2040.
Yet, according to the IEA, today’s supply and investment plans for critical minerals may not be enough to keep up with this growing demand, and organisations across the minerals processing industry are under pressure to drive more efficient production. New regulations from the International Sustainability Standards Board (ISSB) — which will require organisations to accurately track and report on Scope 1, 2 and 3 emissions — only add to the pressure, particularly given how complex and energy-intensive the production of these minerals can be.
A leading scientific organisation recently approached our team to help tackle this issue. They wanted a way to accurately measure the carbon footprint of nickel and cobalt production today through multiple plant configurations, and to investigate the effects of changing production processes to reduce carbon emissions in the future.
Implementing digital tools for measuring emissions
The scientific organisation sought to implement digital tools that would help them:
- Measure a reporting baseline, so they could set targets against it when reporting on initiatives to reduce emissions and waste
- Test scenarios using steady-state simulation technology, so they could investigate the effects of changing processes on the volume of emissions and waste.
Using our sustainability software our team enabled both of these goals.
The first task was to create a reporting baseline and deliver on the primary focus of the project, which was to evaluate the carbon footprint of multiple nickel and cobalt production methods.
To achieve this, we developed two flowsheets on the production of nickel and cobalt from ore — one via a mixed hydroxide intermediate, and the other via a mixed sulphide intermediate. Both options involved an HPAL autoclave circuit. A final option, using a sulphide concentrate to produce the battery materials, was considered. A complex energy balance was performed in addition to the mass balance — including accurate modelling of reaction enthalpies, heat losses to the environment and energy changes through evaporation.
On-site hydrogen, hydrogen sulphide and acid reagent plants were also modelled to gain a complete picture of the site’s water and energy requirements, and carbon footprint.
Using steady-state models to investigate change
Once the models were operational, we investigated the outputs and proposed alternative strategies to mitigate carbon emissions and reduce energy consumption. In our analysis, we considered two flowsheets with four operating scenarios to produce battery-grade nickel and cobalt sulfate salts.
Using our sustainability reporting software, we could accurately create a steady-state mass and energy balance of each option; and we could calculate the intensity of Scope 1, 2 and aspects of scope 3 carbon emissions at each step for all flowsheets. Leveraging the granular reporting capabilities of the sustainability software, we could break down all the individual sources of carbon emissions — including emissions due to carbon evolution from the processing of carbonate ores, reagents, and other chemical reactions (by plant section), power draw, emissions related to reagent delivery, and production and combustion of fuels.
Carbon offsets were also taken into account by considering any carbon capture in tailings facilities and electricity generation from excess steam production from the on-site acid plant.
Armed with all this detailed data, the team could analyse the results and make recommendations on potential Scope 1, 2 and 3 carbon reduction options.
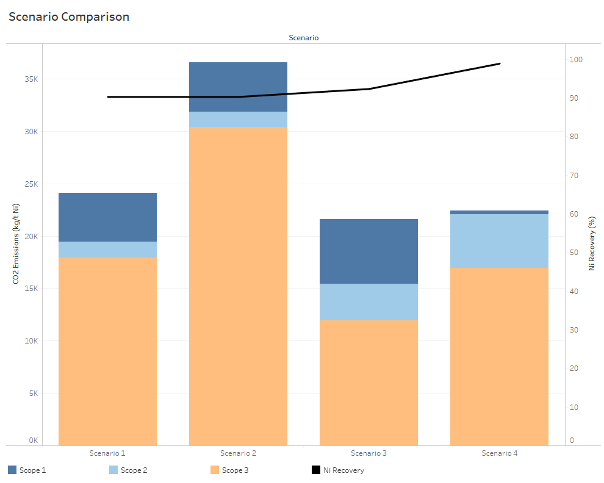
Want to learn more about how our team can help you build steady-state models to drive carbon reduction projects in your industrial facility? Please get in touch.