How our sustainability software provides the digital tools needed to report on sustainability indicators
Industries such as energy, cement, steel, chemical and gas, hydrogen, polymers and manufacturing face unique challenges when it comes to tracking and measuring carbon emissions, waste, water and energy consumption. The challenges they face are closely linked to the complexity of their industrial processes — yet now, more than ever before, these industries are being asked to rise to the challenge.
New global standards – driven by the International Sustainability Standards Board (ISSB) and leading EU bodies, with input from 20+ international governing agencies – will soon require public annual reporting on emissions and demonstrated strategies to reduce them. Other legislation will demand quarterly disclosures on sustainability indicators.
To keep pace with these evolving compliance frameworks, industrial organisations need new ways to track emissions, energy, water and more at a granular level across operations and the supply chain. However, siloed legacy systems and manual processes mean most industrial organisations lack the data and digital tools to achieve this.
This was the case for a hydrometallurgical facility in Africa. The facility sought a new way to capture and analyse data about its carbon emissions to supplement their existing reporting, and ensure they could meet the more stringent requirements of new sustainability reporting regulations with confidence. They also sought guidance on ways to increase visibility across all emissions so they could perform value-driven analysis on how to lower their carbon tax bill. The facility approached our team to help realise these goals.
Centralising data
We worked closely with this facility to implement sustainability software, which integrates seamlessly with existing systems and was customised to their industrial process. The solution centralises and collates data from a range of sources — including plant historians, laboratory management systems, manual entry logsheets and shipping databases.
The facility can also use this data to feed into the solutions embedded dynamic simulation model, which acts as a digital twin for the facility. This digital twin is capable of calculating unmonitored streams, inventories and performance statistics in near real-time, providing even more powerful insights into emissions, water and power consumption.
Most importantly, the solution enables the facility to calculate its Scope 1, 2 and 3 greenhouse gas emissions. Specifically:
- Scope 1 emissions are calculated by analysing fuel consumption and using the digital twin to work out emissions throughout the production process
- Scope 2 emissions are calculated by looking at the consumption of electricity as a whole and at an equipment level
- Scope 3 emissions are calculated by looking at indirect emissions outside the production process through shipping records and plant instruments, such as the emissions associated with the production and delivery of raw materials, and the shipping and processing of final products
By gaining access to all of this granular information, the facility can better analyse and report on its emissions, and keep pace with changing and emerging compliance regulations across different jurisdictions.
Accurate reporting on direct and indirect emissions
With our sustainability software, the facility in Africa can now track and produce auditable reports on all contributors to carbon emissions and plant electricity consumption quickly and easily, in accordance with relevant regulations — from the consumption of fuels to the emissions caused during production processes, through to delivery.
Engineers can now analyse reports to work out why emissions are higher on certain days or across some products, and take action to optimise processes and lower overall emissions.
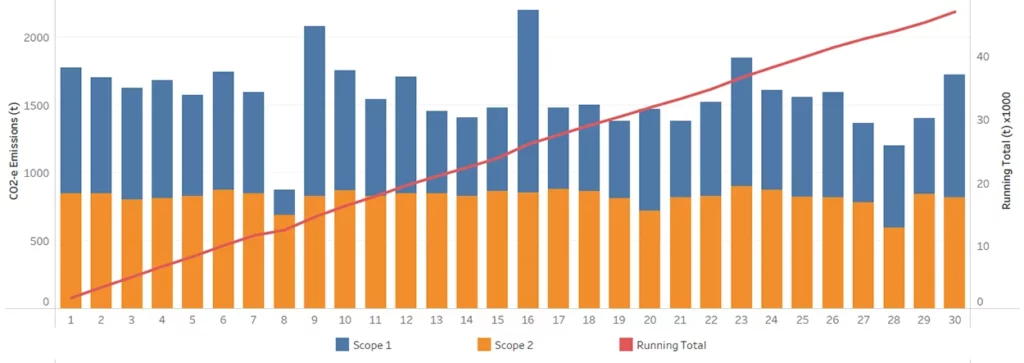
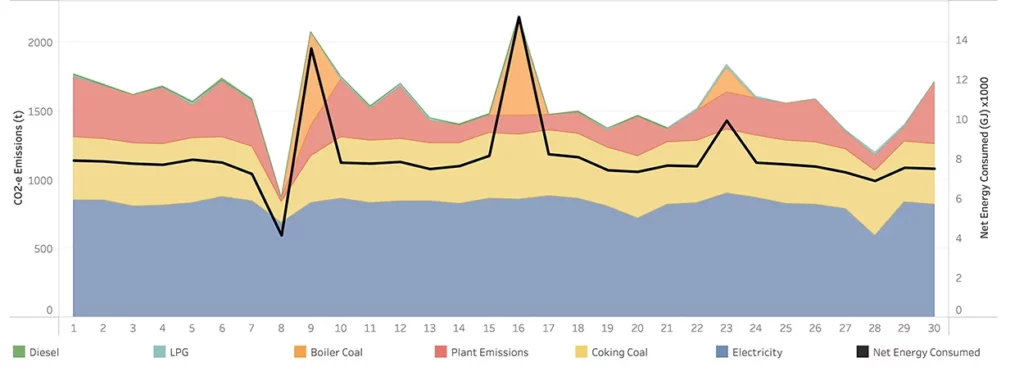
Scope analysis can also be conducted, as indicated by this chart:
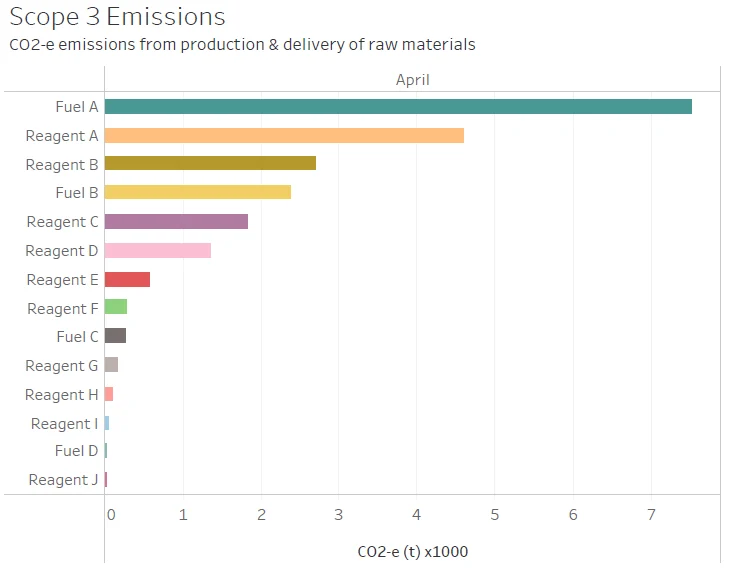
The facility can also dive deeper into upstream impacts on carbon emissions, and make more strategic decisions around suppliers.
Beyond the new mandatory reporting requirements , the facility can also use our solution to track emissions from other potentially hazardous gases, such as NO2 and SO2. Armed with these valuable insights, they can optimise productivity, operational efficiencies, climate footprint and financial returns.
To learn more about how our sustainability software and our team can help you capture, analyse and report on sustainability indicators such as GHG emissions across scopes 1, 2 and 3, water, energy, air quality, waste, hazardous materials, pollutants and nature-related risk factors in your industrial facility, get in touch.